7 Single Point Mooring Offloading Systems
With the exception of an export pipeline (which requires a developed pipeline infrastructure to be cost effective), the offshore production offloading can be performed in two ways: either in tandem mode or through a Single Point Mooring (SPM) system. For large producing fields, the tandem solution is deemed to be too risky as it involves the tankers to stand side-by-side with the production floater while enduring the environmental loads and with the collision risks that may be associated to such an operation. The tandem offloading is hence generally considered as a back-up solution.
The transfer of fluids to tankers through SPM systems is used worldwide but is very developed for deepwater applications in West of Africa, where the use of non-weathervanning (spread-moored) floating production units is feasible and where there is no developed pipeline infrastructure.
The following sections detail the Catenary Anchored Leg Mooring buoy systems used in deepwaters, as well as the emerging HiLoad system (Section Section 7.1, “CALM System Description” and Section Section 7.2, “HiLoad Technology”). The associated export line typical configurations are presented in Section Section 7.3, “Cargo Transfer Vessel (CTV)”.
The main SPM contractors are:
Single Buoy Moorings Inc. (SBM), www.singlebuoy.com
National Oilwell Varco Advanced Production and Loading (NOV-APL), www.apl.com/apl/
Bluewater (shallow water experience only), www.bluewater-offshore.com
Remora Technology (HiLoad system), www.remora.no
![]() | Tip Click these links below for access to 3D resources: |
7.1 CALM System Description
7.1.1 General
The functions of a CALM system, so named for the mooring system that holds the buoy in position, are: (a) to enable transfer of fluids between the production floater and the shuttle tanker and (b) to provide mooring facilities for the tanker.
The CALM system comprises a moored floating buoy, which is anchored to the seabed by an array (typically six lines) of mooring lines connected to seabed piles. One or more conventional nylon rope hawsers (contingency) are used to moor the tanker to the buoy. Hawser should be fixed to the CALM buoy by means of Quick Release Hook for easy hawser operation (i.e. disconnection; maintenance, inspection, etc…). The Quick Release Hook could be activated on local or remote mode.
The oil is transferred between the buoy and the tanker bow manifold by means of a loading/unloading hose line and a tail line.
Figure 7.1 - The Dalia Buoy based on the APL's BTL system (see Section Section 7.1.3, “Turret Buoys”)
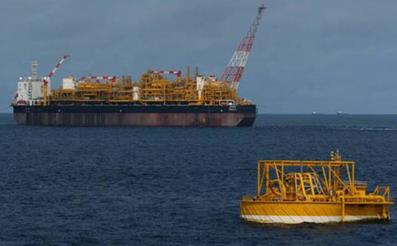
Different concepts of CALM buoy exists, with different slewing bearing positions (see Figure 7.2, “CALM Buoy Concepts”):
Turntable Buoy: buoy with a geostatic fixed buoy body (moored to the seabed) and a rotating mooring table (conventional design)
Turret Buoy: buoy with a geostatic turret and a buoy body, which is rotating around the turret.
7.1.2 Conventional CALM Buoy
The conventional CALM buoy is detailed in the following Figure 7.3, “CALM Buoy Detailed Description (typical)”. It consists of a cylindrical hull fitted with a turntable that will receive the loading/unloading hoses and the mooring hawser connections. A slewing bearing allows the turntable to freely rotate through 360 degrees, thus allowing the tanker to weathervane and take up the position of least resistance to the environmental effects of wind, wave and current.
The 'turntable' type CALM buoy has been used in many deepwater developments (e.g. The Total's Girassol or ExxonMobil's Ehra fields, see figures below).
7.1.3 Turret Buoys
The turret buoy is a weathervanning system which includes a full internal turret. The entire buoy body swivels around the central turret with no external yoke. The bearings and riser line terminations are protected inside the buoy from tanker collision.
The turret buoy system has been used on the Dalia project (Total, WOA). The new APL design features a tail (see Figure 7.7, “The EGINA BTL general and internal turret views”), which provides weathervaning of the buoy and avoids tilt of buoy from hawser tension.
The EGINA BTL system weighs approximately 1000 tonnes and features dimensions of 31m x 20m x 9.0m with an operating draft of 6m. It is moored by means of nine lines connected each to a suction pile.
The system comprises:
Buoy hull
Bearing assembly
Internal turret, including riser line terminations (2 off 18" ID flexibles) and mooring line connections
Mooring lines (9 off) and suction piles (9 off)
7.2 HiLoad Technology
The HiLoad technology (Remora Technology) is currently being developed in order to be an alternative to the traditional moored loading buoys. The claimed advantages are (1) to be independent of the water depth (i.e. no mooring lines connected to the seabed with the DP HiLoad system) and (2) to allow the use of regular tankers or tankers of opportunity without specific equipment onboard.
The system consists in an 'L'-shaped semi-floating steel structure. It is capable of connecting any vessel and the unit is equipped with thrusters that allow to keep both of them on station during the loading operation.
For the connection to the tanker, the unit uses its thrusters to manoeuvre into position relative to the vessel. Once in position, ballast tanks are emptied, bringing the HiLoad soft fenders into contact with the hull bottom (see Figure 7.9, “Connection Sequence”). As the horizontal part of the 'L' is pushing towards the hull bottom, six cofferdams are established by gaskets mounted on the top of the docking unit. The water inside the cofferdams are then drained, the hydrostatic head providing a pressure differential that clamps the unit onto the hull bottom with several thousand tonnes. The areas inside the cofferdams are covered with rubber devices which provide a high friction coefficient with steel.
When connected to the DP loading unit, the tanker is free to weathervane around the centre of the unit. The HiLoad unit then allows the two connected systems to act in DP mode. Position Reference Systems fitted on the unit constantly measure offsets and velocities, with input to the Position Keeping Control System. The HiLoad thrusters therefore allow to keep the tanker in a mean position.
A two phase emergency shutdown process allows to avoid any excessive load in the riser/umbilical system in case of DP failure, by firstly stopping the export pumps and closing the crude line valves and then by disconnecting the DP-Terminal from the tanker.
When no loading operation is performed, the HiLoad system can kept floating at a draft minimizing the environmental loads on the unit.
The offloading system comprises the following main components (Figure 7.10, “Typical Offloading System Overview”):
DP Loading Unit:
Steel Hull
Marine Systems
Fender and Tanker Attachment System
Thruster System
Integrated Control and Automation System
Tanker Loading Hose
Swivel
Electrical Systems
Safety Systems
Oil Transfer Line
Power and Signal Umbilical
FPSO Arrangement:
Oil Transfer Line and Umbilical Terminations
Power Supply
Operation Command Centre
An extensive qualification program has been undertaken in order to qualify the technology. Conceptual design, feasibility study, detailed design and scale model testing were carried out. The tests showed that the system could operate in Hs above 4,5m and could keep very large crude carriers in position in 1-year return conditions based on West Africa metocean conditions. Survival tests were also carried out with extreme wave and wind conditions as measured during hurricane Katrina (Gulf of Mexico, 2005), with maximum wave heights of 30 m in combination with extreme wind speeds of 60 m/sec. The HiLoad DP unit handled these conditions without any significant roll or pitch motion, with a vertical heave motion in harmony with the seas. The system has received Approval In Principle from both ABS and DNV.
In 2012, Norwegian technology specialist Remora has nailed down a 10-year contract plus options with Brazilian oil giant Petrobras to deploy a dynamically positioned HiLoad vessel for offloading from spread-moored floating production, storage and offloading vessels in the Campos and Espirito Santo basins off Brazil.
The technology is also being developed for other applications, such as import and regasification of LNG (TORP Technology) and as a portable DP system for semi-submersibles, ship-shape and circular Sevan vessels.
7.3 Cargo Transfer Vessel (CTV)
Loading of fluid to tankers in open sea may be a demanding operation, particularly in harsh environment. The operation requires dedicated shuttle tankers equipped with dynamic positioning system, excessive thruster capacity and specialized loading systems. Such shuttle tankers are equipped with loading systems, normally installed in the vessel’s bow, enabling the tanker to connect to a floating production facility, a loading tower or loading buoy via a loading hose, and thereby allowing transfer of the cargo to the tanker. The tanker can be moored to the production by a flexible hawser, assisted by vessel’s own thrusters or propellers. The tanker can alternatively be positioned by its own thruster system (Dynamic Positioning System) without any mooring hawser.
The benefit of the Cargo Transfer Vessel is to reduce the investments in extra equipment on conventional tankers, LNG carriers or ships carrying liquids in open sea. It also enable to overcome the main challenge of the conventional tankers being their limited maneuvering and station keeping capabilities.
7.4 Export Lines
The main applications of oil offloading systems involving export buoys are found in West of Africa (lack of pipeline infrastructure, adequate environmental conditions for spread-moored floaters). For safety reasons, these offloading buoys are generally located at about 1,600-2,000m from the production floater to avoid any tanker impact risk. The transfer of product from the floater to buoy is carried out by large diameter suspended flowlines.
The flowlines are generally configured in a double wave ('W') shape by introducing distributed buoyancy along the middle section of the lines.
The use of a 'W' rigid steel pipeline as an export system has been introduced by Total with the Girassol field development. The export system features two 16" steel lines each hung-off by flexible joints at each extremity:
The 'upper' line, which is 2,400m long and is suspended in a water depth of 440-530m
The 'lower' line, which is 2,750m long and is suspended in a water depth of 630-740m
The double wave configuration has also been used in conjunction with flexible flowlines, e.g. for the Dalia development which features two 18½" ID (24¾" OD) flexible lines stabilised by 60 buoyancy module each:
The 'upper' line, which is 2,200m long and reaches a depth of approximately 250m
The 'lower' line, which is 2,275m long and reaches a depth of approximately 385m
An innovation of the Dalia system is to replace the conventional radio telemetry by a fibre optic communication system between the buoy and the FPSO. The flowline system includes optical fibres inserted in four 3/16" carrier tubes located in an armour layer of the upper flexible line.
Same configuration and technology has been used on EGINA field development.
The double wave configuration provides high flexibility to the flowlines to sustain the buoy excursions. It is hence very adequate to the deepwater developments. However, other configurations can be envisaged, such as the simple 'U' catenary shape which has been used for the first time on the Ehra field.
The Ehra offloading line system is composed of two 22" OD steel flowlines. They are suspended between the FPSO and the CALM buoy in a 'U' shape arrangement by flexible joints. The main concern of such configuration is the fatigue performance of the lines, hence a 600m thicker section has been implemented on the buoy side.
The PAZFLOR offloading line system is composed of two 16” ID TRELLINE flexible bonded lines in W shape connected at each extremity to the Buoy and to the FPSO via a Gimble table which allows the decoupling of each OOL from the Buoy and FPSO wave motions.