4 Tie-in Tool Technology Review
4.1 General
The pull-in and connection systems can be divided in two types:
Remotely Operated Tools (ROT).
These autonomous ROT systems can be:
Two tools tie-in system (a pull-in tool and a separated connection tool) or single tool system which combined all the functions. A pull-in tool is designed to pull the line in the structure through series of guides or funnels, lock the line on the structure, release the pull-in head and remove the debris cap; the functions of a connection tool are to position the flowline hub, perform the connection and carry out seal tests.
Designed for guideline or guideline-less installation method.
With subsea winch integrated within the pull-in tool or linear winch on ROT and cable storage drum on tie-in vessel.
ROV-mounted pull-in and connection tools
Above types of tools reflect the historical evolution of the tie-in tool technology:
The first generation was composed by two ROT systems (one pull-in tool and one connection tool)
Single tool ROT, combining both functions of pulling and connecting, were designed as an evolution of the first generation
ROV-mounted tools
Light multiple tie-in tools (TechnipFMC UCON-H, Aker HCS, etc.) represent the latest improvement for deep to ultra-deep water operations.
4.2 Remotely Operated Tools
Almost every SPS manufacturers / subsea contractors have developed their own ROT:
The ROT system can be either two tools system deployed independently, one for initial pull-in operation and one for the connection phase, or one single tool combining both tie-in sequences.
The design maximum operating depth of such tie-in tool is about 500m. They are able to handle both rigid and flexible flowlines.
The main tools and their characteristics are described hereafter:
Schlumberger McPAC.
The McPAC two-tool pull-in and connection system uses a drill-pipe deployed pull-in tool to pull a flowline or umbilical onto a porch structure by means of a surface winch cable, then the connection tool connects the line with a 2-bolt clamp and seal plate assembly. The McPAC system has been used several times on projects such as Shell/Exxon Mobil UMC (UK North Sea), Placid's Green Canyon 29 and Enserch's Mississippi Canyon 441.
Flowline sizes:
up to 16" (flexible and rigid pipe)
Pull-in tool design water depth:
460m
Pull-in tool dimensions (WxBxH):
4m x 3.3m x 5.6m
Pull-in tool weight:
25.5ton
Connection tool design water depth:
850m
Connection tool dimensions (WxBxH):
3.2m x 1.2m x 2.9m
Connection tool weight:
3.7ton
Aker Solutions "TOGI tools"
As per above method (drill rig + lay ship), Norsk Hydro TOGI (Troll Oseberg Gas Injection project) 20" gas trunkline was pulled and tied-in, in 1991, with two ROTs manufactured by Aker Solutions:
Maximum pipe diameter:
20" (rigid pipe)
PLT dimensions (WxBxH):
3.4m x 2.4m x 4.2m
PLT weight:
34ton
Maximum pull-in force:
60 / 120ton
UCT dimensions (WxBxH):
2.9m x 2.7m x 3.9m
UCT weight:
28ton
Schlumberger DISPS pull-in and connection system.
This two-tool pull-in and connection system has been developed by Schlumberger as part of BP Exploration's DISPS project. It is run on drill-pipe and includes a pull-in tool, a connection tool, a clamp connector and a piggable termination cap.
Flowline sizes:
up to 12" (rigid pipe)
Design water depth:
730m
Pull-in tool size (WxBxH):
2.4m x 2.2m x 4m
Pull-in tool weight:
9.2ton
Connection tool size (WxBxH):
2.4m x 2.2m x 4m
Connection tool weight:
14.8ton
Aker Solutions PICT (Pull-In and Connection Tool).
The PICT is a single trip tool that combines the pull-in, by means of linear winch and pull-in cable coming from surface, and connection functions. The benefit, against two tool systems, is saved operational time related to less launching and recovery time. It is a field proven system that has been used extensively on Norsk Hydro Troll (approximately 300m) development for tie-in of ISU umbilical and up to 10" flexible flowline.
Maximum pull-in capacity:
30ton
PICT main dimensions (WxBxH):
3.2m x 3m x 4.5m
PICT weight (in air):
10ton
Flexible pipe size:
10" (maximum)
Water depth:
500m
TechnipFMC UTIS.
The TechnipFMC Offshore ‘Universal Tie-In System’ (UTIS) is a combined pull-in and connection tool, designed to perform connections of steel lines of up to 14" OD and flexibles of up to 12" ID. It has successfully performed tie-ins of flexible flowlines at Zaphiro field phase 2 (500m). It was also used for tie-ins on Statoil Statfjord North and East Snorre fields.
Maximum water depth:
2500m
Pull-in force:
40ton
Pull-in speed:
0 – 15m/min
Max. stroking force capacity:
65ton
UTIS footprint:
1.4m x 1.8m
UTIS Height:
4.9m (including tool control unit)
UTIS weight (in air):
14.4ton
UTIS weight (in water):
12.4ton
Exxon Zinc Pull-in and Connection System
This system was developed to connect the two 8" export flowlines and the 4" service line to the Zinc subsea template. It is able to perform pull-in, connection and pressure testing using subsea winch and ROV-conveyed modules (i.e. neutral buoyant connection tool to be positioned by ROV).
Flowline sizes:
<10" (rigid pipe)
Design water depth:
460m
4.3 ROV-mounted Pull-in and Connection Systems
The ROV mounted pull-in and connection systems are typically composed of both pull-in and connection tools, which is deployed by ROV. The tool skid is mounted under the ROV main frame and an interface tie-in porch is integrated onto the subsea structure. All these tools can be operated by means of a working class ROV deployed from a conventional ROV support vessel.
The ROV mounted tools have the following general characteristics:
Maximum pull-in force: 30ton
Pull-in distance: from 3m to 40m
Angular alignment: +/-15°
Tool weight: 8-10ton
They are able to handle flexible lines up to about 20" and small diameter rigid pipelines (depending on the required pull-in force).
The main contractors/ROV mounted tools are:
TechnipFMC (Rovcon & Flexconnect tool)
Subsea 7 (Dmac)
Aker Solutions (RTS)
SAIPEM (Sonsub DFCS)
GE (Vetco Icarus)
The following paragraphs provide details for each tool:
Technip's Flexconnect (versions II and III)
The Flexconnect II system was developed in year 2000 to perform horizontal clamp connections from 6" to 16" flexible flowlines at 500m water depth. The system includes a Pull-In and connection Module (PIM) that is deployed to the seabed in a workbasket. A ROV-deployed service skid is used to wet mate the PIM subsea. The system features two 15 Te (each) pull-in winches and two 15 Te top cylinders to pull the termination head. It also includes a set of robotic tooling for hub seal replacement, hub inspection and cleaning.
The flexconnect has been used to perform different types of connections (Norwegian sector), including pull-in and connection of flexible and rigid spool-pieces, flextails, etc.
The Flexconnect III is the latest development by Technip to allow deepwater intervention with wider size range of connections. The system features the ability to perform both on-structure and on-seabed connections from about 2" (e.g. gas lift jumper, methanol line) up to 30" (export line connection).
The methodology and equipment are as follows:
On-structure system
The on-structure type of connection refers to items deployed directly onto the structure and which does not contact the seabed. A large guide-pin is provided on the porch structure for primary guidance. Once it is engaged, vertical guide slots on the structure provide secondary guidance of the Stroke-In Module (SIM). The SIM is lowered down into position and locked off.
A Seal Tooling Module (STM) can then be used for seal change-out, inspection and cleaning operations. The outboard hub is stroked into the fully engaged position and the clamp closed using a torque tool and integrity of the connection tested.
The standard equipment includes a ROV deployed service skid fitted with integral wet mate for tooling interface and a workbasket containing the STM, torque tool and external seal test tool. For on-structure connection, the SIM is also used, deployed (with the spool) and recovered on a spreader bar.
On-seabed system
The flexconnect III uses two separated modules to perform on-seabed connections: a Pull-In Module (PIM) to pull the connection head to the structure and a Stroke-In Module (same as described above for on-structure connections) for the final stroke and connection.
The on-seabed operation involves the deployment of the rigid or flexible spool-piece onto the seabed within predefined target boxes. The workbasket is deployed to the seabed with all required tooling. The ROV docks onto the SIM in the workbasket and then install it onto the porch structure. The PIM, which contains the winching unit, is then used to pull the termination head into place on the SIM. The termination head is then clamped by the SIM and the PIM released and returned to the workbasket. The procedure then continues similarly to the on-structure connection.
TechnipFMC Rovcon
The ROV based Tie-in & Connection System Rovcon is designed for both first-end and second-end tie-in of Flowlines and Umbilicals. The system is attached underneath a work class ROV. The tie-in skid package performs tie-in using two winches, while final pull-in and closing of the connector is done by means of stroking cylinders. The system comes with a set of ROV operated tools for hub preparation prior to connection.
The Rovcon (Mk2) system main features are:
Tie-in Tool Overall Dimensions: Length: 3,200 mm
Width: 1,850 mm
Height: 1,750 mm
Tie-in Tool Weight, In air: 3,0000 kg
In water with Buoyancy: 30-50 kg
Flying Interface Weight, In air: 600 kg
In water w/buoyancy: 50 kg
Hydraulic supply from ROV, Pressure: 207 bar
Flow: 40 l/min
Pull-in Force: 210 kN (2 x 105 kN)
Stroking Force: 660 kN
Alignment Force in each Axis, Vertical: 732 kN
Horizontal: 512 kN
Maximum Water Depth: 3000 m
Subsea 7 (Dmac)
The "Fuel Subsea Engineering & Costain" tie-in system is designed for 1500m water depth and flowline sizes up to about 12". It consists in a ROV tool (including torque tools, seal plate replacement tool, hot stab and pressure test tool), a line pull-in tool, interface skid and connection porches mounted on subsea structure. It has been used on the Foinaven field, West of Shetland in 1995 and the Schiehallion field in 1998.
Figure 4.9 - ROV mounted with DMaC interface skid and pull-in & connection module, by courtesy of Subsea 7
Aker Solutions (RTS)
The ROV operated Tie-in System (RTS) consists of a pull-in and connection tool mounted on a standard work class ROV via the ROV interface skid. This tool is composed of the following main items:
15 tonnes Pull-in winch with pull-in rope and anchor
Jack screw torque unit
Termination orientation system
Termination lockdown system
Receiver funnel
Outboard hub alignment clamps
ROV panel
Flexible flowline size: up to 12"
Design depth: 1500m
The Aker Solutions RTS have been used in particular on Norsk Hydro Njord (1998) and Visund (1999). It allows performance of first and second end horizontal connections, for umbilicals, flexible or rigid lines.
SAIPEM (Sonsub DFCS)
The DFCS is a tooling package powered and operated by work-class ROV. It is used to retrieve, pull in and connect pre-laid subsea flowlines or umbilicals. The Sonsub system has been developed for tie-in operations at Amoco's Liuhua 11-1 field in 310m water depth (6" and 13.5" flowlines) and has for instance successfully completed 6-inch flexible flowline tie-in on the Osprey P8 wellhead for Shell UK Exploration and Production in the North Sea.
Flexible flowline: up to 16"
Water depth: 500m
BHGE (ex Vetco Icarus)
ABB/Vetco has developed an ROV mounted pull-in and connection tool similar to the above Aker Solutions RTS.
The Icarus pull-in system was developed to connect the jumpers on the Chevron's Kuito field in Angola.
4.4 ROV-mounted Connection Systems
Some tie-in operations based on direct stab-in of the connector require a much simpler ROV mounted tool, since the pull-in winch system is not required anymore.
These tie-in operations can be basically described as follows:
a rough positioning of the outboard hub is performed by means of hub's torpedo mating the corresponding funnel (for further details, see section 5.5 "Vertical stab, hinge-over and lay-away")
then the ROV-mounted connection tool aligns and mates the two hubs (outboard hub is translated by tool onto the inboard hub)
the connection is performed (with either a collet or clamp connector)
Figure 4.13, “ROV mounted tool connection sequence” further depicts the ROV-mounted connection tool operation (herein represented with a clamp connector).
The ROV mounted connection tools are available from the main SPS contractors such as:
Schlumberger
TechnipFMC (e.g. Girassol, Rosa-Lirio, Pazflor)
Aker Solutions (e.g. Dalia)
This tie-in method is valid for:
flexible and rigid pipe: all diameter (API 5L)
water depth: limitation only with ROV depth capabilities, e.g. 3000m
first end initiation and lay-away
flexible jumpers
rigid spool jumpers
The ROV mounted connection tool have been used mainly in GOM (BP Pompano, BP Troika, Shell Mensa, etc.), in West of Africa (e.g. Girassol, Rosa Lirio, Dalia, Bonga, Erha) etc.
4.5 Light modular connection systems
In the pictures below are presented FMC old and new tie-in systems.
UCON-H connection system has been used on following recent TOTAL projects: Laggan Tormore and CLOV.
In the picture below are shown FMC UCON-H tie-in system and associated tooling and caps.
A video showing main steps for connecting a UCON-H collet connector on a Template Manifold is shown on following YouTube video:
https://www.youtube.com/watch?v=WGiVA4A-EpY
AkerSolutions HCS connection system
Here below are shown the installation sequence for a rigid spool fitted with AkerSolutions HCS connector and ROV tooling.
Aker Solutions VCS connection system
In the picture below is shown AKER VCS tie-in system with associated ROV tooling.
BHGE (ex VETCO) VCCS tie-in system
In the picture below is shown BHGE VCCS tie-in system.
4.6 Flange Diverless Tie-in Tool
MATIS system
Acergy (Stolt Comex Seaway at the time), and partners Hydra-Tight Ltd. and National Hyperbaric Centre Ltd., developed the Modular Advanced Tie-In System (MATIS). MATIS research has been initiated in 1994 and first was successfully demonstrated in 1997.
The MATIS system was used offshore for the first time on the Statoil Loke field in 1999. Stolt Offshore has also installed standard flanges for a number of projects offshore Norway before successfully completing 52 flange connections in up to 1450 m of water for the Girassol project, offshore Angola in 2001. The Girassol installation program included connection of 39 flanges in the horizontal position, on the top of the flowline sleds, and 13 flanges at the base of the riser bundle towers, which were in the vertical position. The program used two sizes of flange, 9 in. and 13 5/8 inch, both standard API with a 5,000-psi pressure rating.
Figure 4.22 - MATIS on its skidding system and during launched operation, by courtesy of Acergy (now Subsea 7)
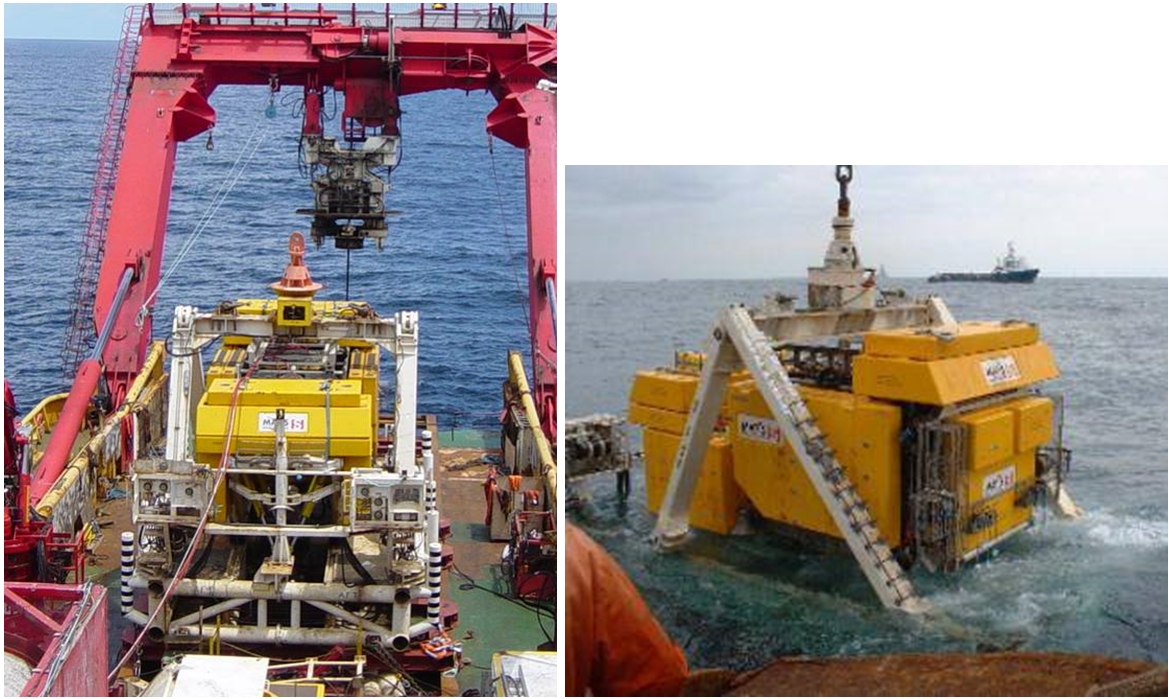
MATIS can connect flanges within the range of 4-36 inch in diameter, with a maximum depth rating of 3000 m. Different MATIS systems exist, for deep and ultra-deepwater application, product name is called DeepMATIS system where all tie-in functions are gathered in one single tool called DeepMATIS Tool that performs flanges alignment, mating, seal insertion, bolts and nuts insertion and tightening.
Many tool sub-assemblies fitted inside the DeepMATIS Tool are designed and used only for a specific flange size and need to be replaced on-deck if connections for a different flange size are needed.
The DeepMATIS is deployed separately from the ROV to the seabed by using a MATIS launch frame (MLF), and then the ROV equipped with a ROV dedicated interface Skid (RIS) docks onto the MATIS Tool and transports it above the two flanges to be connected.
The ROV interface Skid (RIS) is developed to fit a specific ROV.
Spools are pre-installed and coarse alignment of the spool is achieved with a set of flange catchers welded on the flowline structures.
The DeepMATIS is equipped with 4 reaction claws at its base that locks onto the static structure (SLED for example) and allows aligning the DeepMATIS tool against the inboard flange. The DeepMATIS is also equipped with an alignment claw that will grip the spool and manoeuvred it in order to align the two flange faces.
Once the flange faces aligned, the gasket is inserted, the studs and nuts are loaded into the connection system using the pick-and-place arms. The unit then tensions the flanges and runs the nuts onto the studs in a crisscross pattern. DeepMATIS allows to load all bolts simultaneously and to check the residual bolt load and distribution without any diver intervention.
Flange tooling makes these types of remote connection complex. In comparison with the TechnipFMC collet connector based system, the MATIS system was shown to be large and complex, requiring installation vessel equipped with A-frame or large capacity crane for deployment of MATIS tool. Connection times were long in comparison with the TechnipFMC system (23 hrs vs. 5 hours – ref. OTC 14171).
In addition to Acergy (now Subsea 7), Sonsub (now SAIPEM) had also developed a diverless flange connecting tool called the BRUTUS system.
BRUTUS system
The BRUTUS system conceived by SONSUB (now SAIPEM) in 1997 was used for the first time in 2000 for Statoil Norne Heidron project in North Sea. The BRUTUS system can connect flanges within the range of 8-26” in diameter.
The BRUTUS system includes the following main tools.
A large force pull-in tool called the axial force tool (AFT) aimed at applying the required force to stroke the spool flange toward the connection point within an envelope that allows for reasonable angular and linear errors in the spool's metrology, fabrication, and installation.
A so-called reaction tool (RT) used as a remotely operated vehicle (ROV) -installable and -removable tie-in porch structure, the size of which can be changed as a function of the available space on the relevant subsea structure.
A flange connection tool (FCT) that can perform the rotational alignment and connection of the flanges using standard bolts and tensioners.
In addition, a suite of tooling and ancillary equipment to perform all required subsea operations is also considered as part of the system.
ROV interface skid, allowing each tool to be fitted with standardized interface points, which include mechanical, electrical, and hydraulic interfaces.
A set of pipe-handling equipment such as H-frames, pipe trestles and winches to ease spool positioning onto the seabed.
A set of standard ROV tooling, including a flange/hub cleaning and inspection tool, flange splitters, a seal-replacement tool and a metrology system.