7 Hot-Tap Tie-in
A hot-tap operation aims at installing tee-branch and valves on a ‘live’ pipeline (still producing while hot-tap is being performed) in order to allow future line connection. The particularity of such tie-in is that it is performed on an existing/producing line which was not initially provisioned for such connection.
Two types of hot-tapping methods are available:
Mechanical hot-tap clamp
Hyperbaric hot-tap
The conventional hot-tap techniques use a clamp to be installed by diver around the pipe. Following sealing (e.g. grout injection) of the mechanical clamp onto the pipe, the hot-tap work can commence.
This report will only describe the latest technique of hot-tap based on hyperbaric welding, which consists in welding on the pipeline a tee reinforcement piece.
Thereafter a vertical valve assembly is mounted onto the tee for subsequent trepanning (or hot-tap) through it. A typical (diver assisted) hot-tap outline procedure is described below. This procedure and the figures are extracted from the hot-tap operation performed on the TOTAL's Frigg UK 32" Gas Trunkline in order to connect the Talisman Energy Ltd Ross 6" Gas Export Line (1998).
Figure 7.1 - Hot-tapping machine and protective structure (lower part) installed on the Frigg Gas Export Line
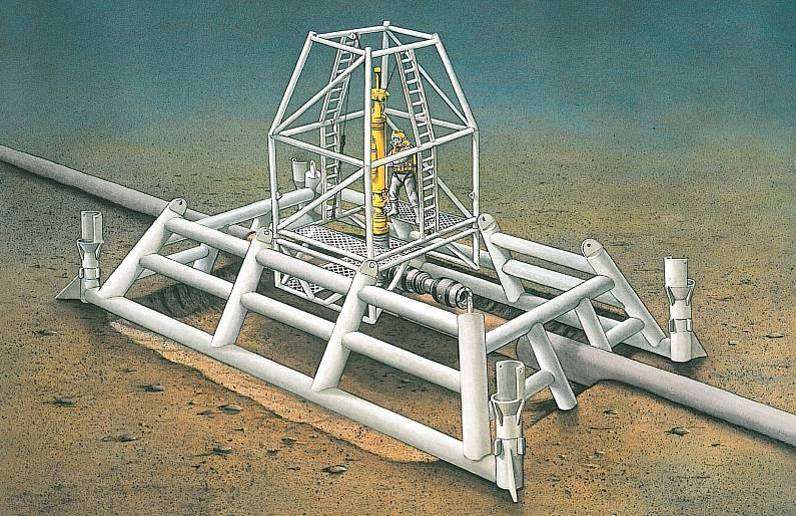
A typical outline procedure would be as follows:
Hot-tap location
Locate the pipeline and the pre-determined hot-tap location (e.g. pipe wall residual thickness)
Clear and excavate the seabed for welding habitat installation
Remove the pipe coating (e.g. high pressure jetting, concrete wire cutter)
Protective structure installation. The structure has a dual function: (a) as a working template (tee branch installation, habitat support, etc.) and (b) as a protective structure of the tee branch plus valve and piping assembly; once the tie-in has been performed.
Welding operations (see Figure 7.2, “Installation of welding habitat” and Figure 7.3, “Hyperbaric hot-tap welding & assembling process”)
Deploy and prepare the habitat (e.g. including the welding and heating modules)
Final cleaning and detailed inspection of the designated hot-tap area (Figure 7.3, “Hyperbaric hot-tap welding & assembling process”, step 1)
Fit and weld the tee branch and reinforcement sleeve (Figure 7.3, “Hyperbaric hot-tap welding & assembling process”, steps 2 to 4)
Weld the valve assembly (step 5)
Test, re-instate the coating and demobilise the habitat
Hot-tap operations (see Figure 7.4, “Hot tap outline operation”)
Deploy the support frame with the tapping machine (see Figure 7.1, “Hot-tapping machine and protective structure (lower part) installed on the Frigg Gas Export Line”)
Install the tapping machine, purge it and open the tee branch ball valve
Perform the cut, retract the cutter with the coupon and close the valve
Depressurise the tapping machine and recover the hot-tap equipment
Note: For the Ross hot-tap project, a maximum pressure in the Frigg pipeline of 80 bars (i.e. flow reduction) at tie-in location was required during around 5 to 7 days.
Valve / spool piece installation and work completion
Install various equipment (valves, end caps, etc.) required for the future spool tie-in
Install the protective structure roof
Clear the site and carry out as-built survey.
This operation is generally made with diver assistance and as such cannot be considered as a deepwater operation. However, some contractors are now developing diverless hot-tap systems, e.g. the Deep Tap alliance (Oil States (Houston), Williams, Oceaneering, and T. D. Williamson), Clear Well Subsea, IKM.
Most advanced diverless hot taps machine like remotely operated TDW Subsea 1200RC tapping machine can be used for installing hot taps in water depths of up to 3,000 m.